ЯК ЗА ДОПОМОГОЮ МЕТОДОЛОГІЇ ТОС МИ ПЕРЕСТАЛИ ВТРАЧАТИ ДЕСЯТКИ ТИСЯЧ ГРИВЕНЬ НА ГОДИНУ
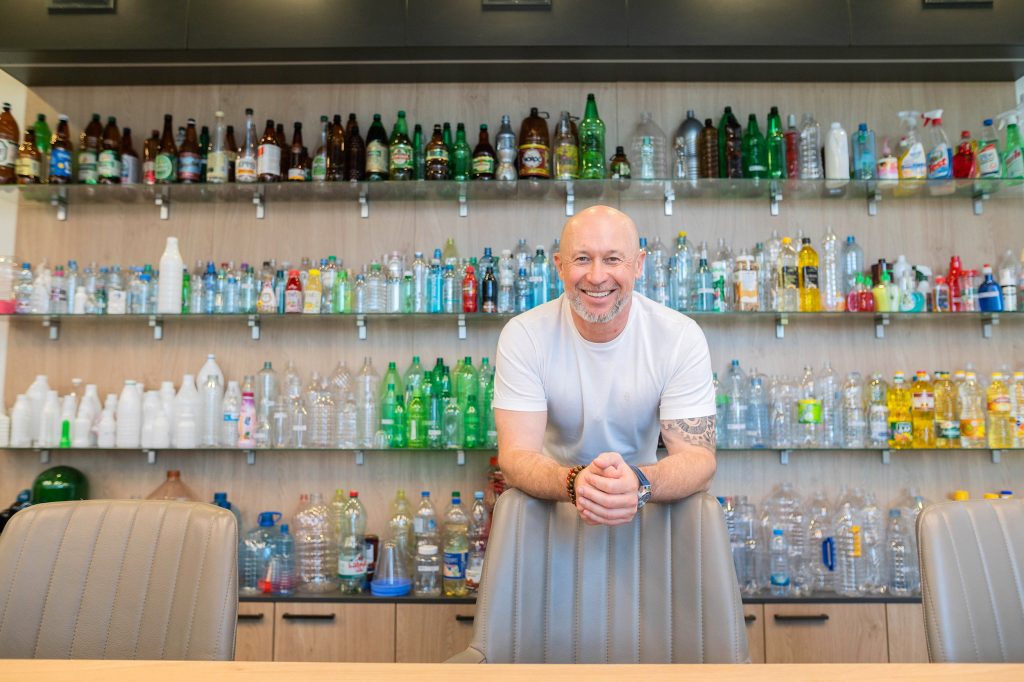
Що найбільше заважає розвитку компанії? Можна назвати багато різних причин, але одна з основних – шаблонне мислення її керівника. Я переконався у цьому на власному досвіді, коли кілька років тому нашу компанію Pet Technologies зациклило в порочному колі: спочатку не можемо продати, потім не можемо виготовити, далі знову не можемо продати і так по колу.
Ми випускаємо складне обладнання. Через тривалий цикл виробництва після того, як ми заключили контракт, формуємо план на пів року вперед. Продали, завантажили виробництво, і раптом виявляється, що ми не можемо своєчасно виконати замовлення. Звичайне мислення в такому випадку штовхає нас до збільшення кількості працівників, верстатів і запасів на складі. Збільшуємо виробництво на 5%, а проблеми залишаються – у швидкості нічого не змінюється.
Це шаблонне мислення: щоб збільшити виробництво і заробити більше грошей, нам потрібно купити більше верстатів і найняти більше людей, збільшуючи витрати. Мислення поза шаблоном полягає в тому, щоб знайти вузьке місце у виробничому процесі, де втрачаються час, сили і гроші, та працювати з ним.
Самостійно змінити погляд на процес керівнику і його команді неможливо – потрібна допомога ззовні. Нам допомогли консультанти, що спеціалізуються на впровадженні управлінської методології ТОС (Теорія Обмежень Системи). Це складна багаторівнева методологія.
Якщо простою мовою, її суть зводиться до двох речей. Перша: знайти «вузьке місце» та підвищити його ефективність. Друга: робити тільки те, що потрібно саме зараз.
Як це спрацювало у нас?
Знайшли вузьке місце і вивільнили ресурс
Перед тим як консультанти приїхали на завод для вивчення ситуації, мені порекомендували прочитати книгу «Мета» Еліяху Голдратта, автора системи ТОС. Книга написана чудово – у жанрі роману. Історія розповідає про керівника підприємства, який крок за кроком виявляє та усуває вузькі місця на виробництві, таким чином рятує бізнес і досягає чудових фінансових результатів. Книга цікава, але мені здалося, що написане у ній не спрацює в наших реаліях – я взагалі насторожено ставлюся до закордонних практик. Система, на мою думку, ефективно працює у тому середовищі, де її створили.
Ще більше мене насторожили консультанти, які справили враження ідеалістів-космонавтів, далеких від реального виробництва. У їхньому плані, складеному після вивчення нашої ситуації, було багато гарних ідей. Однак я не розумів, як їх можна реалізувати на практиці. Мій скепсис швидко розвіявся, коли ми зайнялися пошуком РОМа. РОМ – це ресурс, що обмежує потужність. Та сама «пляшкова шийка», яка гальмує процес, незалежно від кількості верстатів і людей, залучених до виробництва. Знайти РОМ непросто – для цього збирається велика кількість статистичних даних. Ми шукали кілька тижнів.
Нашим вузьким місцем виявився великий фрезерний обробний центр, на якому ми працюємо з габаритними деталями. За логікою ТОС, це ланка, що обмежує прохідність всієї компанії. Перший етап роботи з вузьким місцем – це збір статистики. Ми поставили співробітника поруч із цим верстатом, і він кілька тижнів із секундоміром фіксував дані у три колонки: працює, переналагоджується, простоює. Через тиждень ми подивилися на цю таблицю. Вийшло: працює 30% часу, переналагоджується 30% і 40% простоює. На перший погляд, ну і що з того. Поки не починаєш рахувати.
Візьмемо середню українську компанію з річним оборотом 450 млн гривень. Одна робоча година у такій компанії коштує 200 000 гривень. Якщо 40% робочого часу втрачається, це еквівалентно 80 000 гривень. Усвідомлення цього мотивує зробити все можливе, щоб скоротити час простою (все одно верстат простоюватиме – він не може працювати без зупинки). Але якщо з цих 40% хоча б на 20% його дозавантажити, то можна вдвічі скоротити втрати.
Перше, що ми зробили — оптимізували переналагодження, забезпечили наявність необхідних інструментів і обладнання безпосередньо біля верстата. До оператора приставили асистента, який допомагає з подачею і переналагодженням деталей. Він виконує всі супутні завдання, щоб оператор не відволікався.
Ми з’ясували, що верстат часто простоює через відсутність креслень. Тепер всі креслення знаходяться на місці у двох примірниках, щоб не загубилися. Якщо виникає технологічне питання, робітник може викликати технолога за допомогою кнопки.
Обід також оптимізували — майстер обідає прямо біля верстата, поки обробляється велика деталь (це займає близько 20 хвилин). Якщо йому потрібно відійти, асистент стежить за процесом обробки деталі.
Для кращого контролю ми також встановили на верстат сигнальний маячок і програму, яка запускає сирену, якщо шпиндель не працює більше п’яти хвилин. Крім того, повісили камеру, яка транслює зображення верстата на екран у моєму кабінеті, кабінетах начальника виробництва та виконавчого директора компанії.
Що це нам дало? Ми вивільнили близько 5% часу з переналагодження. Час простою скоротили вдвічі – до 20%. Середній цикл виробництва звичайної машини на той момент складав 90 днів. Завдяки ТОС ми скоротили цей термін до 45 днів.
Навчилися робити тільки те, що потрібно в даний момент
Ще один важливий постулат філософії ТОС полягає в тому, щоб виконувати лише ті дії, які актуальні на цей момент.
У чому суть? Це дозволяє скоротити запаси на складі, вивільнити час і гроші, щоб використовувати їх більш ефективно. Будується діаграма, яка показує, коли замовлення повинно бути виконане. Від цієї точки відраховується, скільки часу потрібно для кожного етапу. Наприклад, якщо на складання потрібен тиждень, то за тиждень до відвантаження всі деталі мають бути на місці.
Деталі для виробництва повинні надходити за місяць, за тиждень і за три дні відповідно. Але не все одразу, оскільки це створює напруження в системі і хаос. Вивільняються гроші — вони більше не заморожені в запасах і можуть бути використані більш ефективно у потрібний момент.
Звичайно, це викликає нервовість, закупівельники хвилюються, але ми кажемо: «Чому хвилюватися? Термін поставки зрозумілий — два тижні, плюс чотири дні на буфер. Що вас не влаштовує? У чому проблема?» Вони відповідають: «А раптом щось станеться?». Ми кажемо: «Коли станеться, тоді й будемо говорити».
Ці зміни далися нам нелегко, оскільки ми звикли працювати за планом на місяць, два і навіть шість місяців вперед.
Класична ситуація: у токаря є завдання на 15 деталей одного типу, п’ять деталей другого типу і по одній деталі інших типів. Як він спланує свою роботу? Звісно, спочатку він зробить 15 деталей, потім переналаштується на ті, яких п’ять, а потім вже виготовить ті, яких по одній. Неважливо, що більшість деталей першого типу знадобиться нам лише через три місяці.
Відповідно до вимог системи, ми впровадили на виробництві маркування всіх креслень. Креслення з чорним кольором означають, що робота має бути виконана негайно. Червоний колір означає терміновість, але не першочерговість. Зелений колір — це робота в звичайному режимі.
Раніше у кожного робітника була велика пачка креслень на день, на два, на тиждень або місяць, і він сам обирав, що йому зручніше робити. По суті, цим має керувати майстер, а не робітник. Він на свій розсуд обирає та роздає своїм робітникам деталі, вони щось роблять, збирають, не замислюючись над актуальністю — це не їхня задача.
Виробництво стає чорною скринькою: замовлення надійшло, машина вийшла, а що відбувалося всередині — ніхто не розуміє. Хтось робить те, що потрібно сьогодні, хтось — те, що знадобиться через тиждень.
Дотримуючись правил ТОС, ми вилучили всі старі креслення та видали нові — за кольоровими пріоритетами. Потрібно було пів року, щоб люди прийняли нову модель роботи. Правило «не роби наперед, а роби лише те, що потрібно зараз» виявилося найскладнішим для нашої компанії та наших співробітників. Деякі з них просто мусили стояти без діла. Якщо роботи немає, то вони нічого не роблять.
Якщо раніше оплата праці була прив’язана до виробітку, то тепер ми перевели людей на ставку. Досвідчений токар із 20-річним стажем казав: «Як я можу стояти без діла? Я ж не зароблю». Ми відповідали: «Ти отримуєш ставку». Але багато хто довго не міг звикнути та прийняти це. Деякі навіть ховали заготовки, щоб чимось зайнятися у вільний час. Ми запропонували їм у «період простою» дивитися фільм про теорію обмежень.
Не дозволили колективу поховати ініціативу
Я швидко зрозумів, що успіх залежить від волі першої особи. Якщо перша особа компанії не візьме на себе контроль впровадження і не покаже, що це дуже важливо, то нічого не вийде. Я бачив це на прикладі мого колеги. Він самоусунувся на початковому етапі впровадження змін, мовляв: «Розбирайтеся самі». У результаті колектив поховав ініціативу.
Розуміючи, що колектив може протистояти змінам такого рівня, я вирішив особисто бути присутнім на всіх теоретичних сесіях і контролювати практичне впровадження.
Щотижня я разом із начальником виробництва, майстрами та технологами підходив до кожного верстата і запитував у кожного робітника: «Що ти зараз робиш? Покажи креслення». Робітник показував чорні й червоні креслення. Я питав: «Якщо робиш зелене, а приходить червоне, що будеш робити?». Він відповідав: «Переключуся на червоне». Я уточнював: «А якщо чорне?». Відповідь була аналогічною. Якби я прийшов один або два рази, нічого б не спрацювало. Я ходив туди щотижня протягом пів року. Кожен робітник мав зрозуміти, що це не жарт і буде контролюватися до найменших деталей. Лише так інновація стає не тимчасовим рішенням, а філософією компанії.
Результати
Перший результат ми отримали приблизно через пів року. Нам вдалося скоротити термін виробництва серійних машин удвічі, зменшити запаси на складах щонайменше на 20%, і нарешті навести лад у процесі закупівель.
Усього цього ми досягли без додаткових інвестицій і без нових верстатів. Головне в ТОС — це суворо дотримуватися правил, без креативу та самодіяльності. Наприклад, регулярно та ретельно збирати статистику, хоча це нудний і нецікавий процес.
Якщо статистика збирається неправильно, у вас немає даних про роботу системи, і ви не можете знайти причини проблем. Слідкувати за тим, щоб РОМ не переміщувався в інше місце. Це може статися, якщо ви послабите контроль за процесами і не будете приділяти належної уваги тій же статистиці.
За ТОС ми працюємо вже близько десяти років. За цей час багато що змінилося. Наприклад, продукція стала складнішою, що позначилося на процесах. Є речі, побачити які можуть лише люди ззовні, у яких свіжий погляд. Саме тому час від часу ми запрошуємо консультантів, які допомагають відкоригувати процес, підтягнути там, де розхиталося, зламати шаблони, якщо вони встигли сформуватися — а це неминуче, як у виробництві, так і в житті.